こんにちは、東大阪で真空装置や真空部品に50年以上携わってきた真空屋です。今回は、真空絶縁碍子の故障事例を振り返りながら、高性能化のために必要な具体的なポイントとその対策方法を、僕の実体験も交えて詳しくお伝えします。
真空絶縁碍子の重要性とその役割
真空絶縁碍子って普段は地味な存在ですが、実はこれが故障すると装置全体が停止してしまうほど重要なパーツなんです。僕自身、過去のトラブルで痛い目にあった経験があります。
よくある故障1:絶縁破壊とは?
まず一つ目は「絶縁破壊」。碍子が高電圧に耐えられなくなり電流が漏れる現象で、主な原因は材料選定や表面処理の不備です。
失敗から学んだ材料選定の重要性
以前、新しい素材を導入した際に十分な耐電圧試験を行わなかったため、すぐにトラブルが発生しました。結局、高アルミナセラミックスに戻して解決しましたが、この経験から基本を守ることの重要性を痛感しました。
よくある故障2:クラック(ひび割れ)の原因と対策
次は「クラック」です。製造や取り付け時に過剰な締め付けや微妙なねじれが原因となり起きます。僕も過去に取り付け時のトルク管理を怠り、すぐに壊れた苦い経験があります。それ以来、トルクレンチで厳密な管理を徹底しています。
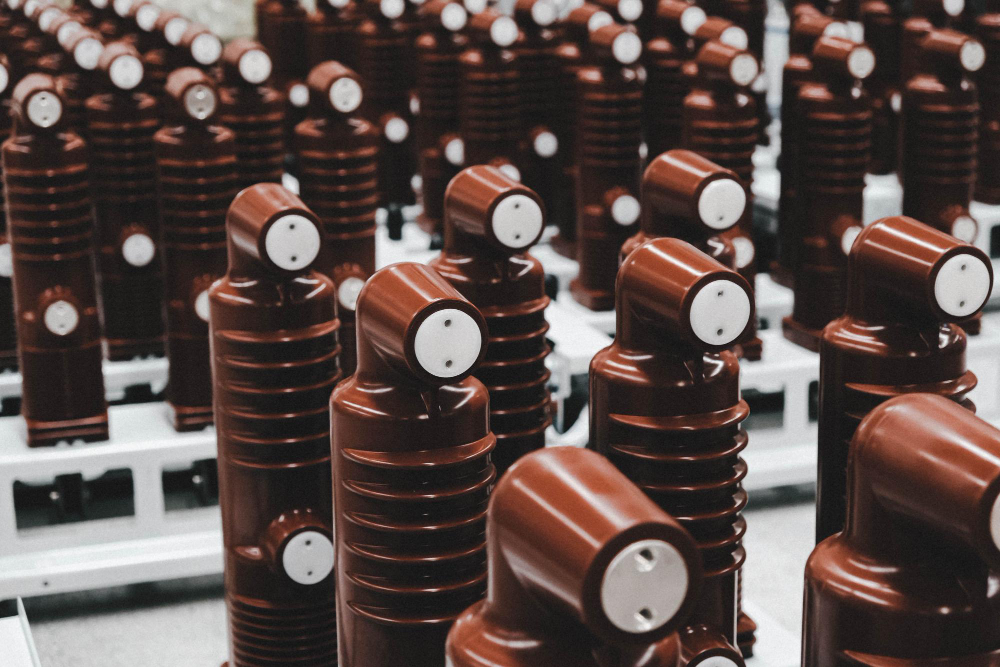
真空絶縁碍子を高性能化する3つのポイント
- 材料選定のコツ
絶縁性能を高めるには、高アルミナセラミックスや窒化アルミニウムなど、耐電圧性が高く真空環境に強い素材を選ぶことが不可欠です。 - 表面処理で絶縁性を向上させる
表面が滑らかでないと微細な放電が発生しやすくなります。ダイヤモンド研磨などの特殊なコーティング処理を施すことで、絶縁耐圧を飛躍的に向上できます。 - 形状設計の工夫が鍵
碍子の形状は絶縁性能に大きく影響します。特に電界集中を避ける丸みを持たせた設計を採用すると性能が格段に向上します。
具体的な改善事例のご紹介
あるメーカーからの相談で、頻繁に碍子が故障している問題を調査した結果、絶縁耐圧不足と表面処理が原因と判明しました。そこで素材を高アルミナ系セラミックスに変更し、表面をダイヤモンド研磨で鏡面加工、さらに電界集中部分を丸みのある形状に設計変更した結果、耐久性が大幅に向上し、故障率も激減しました。
今後の真空絶縁碍子の展望と可能性
半導体や医療機器、宇宙開発など高度な真空環境が必要とされる分野では、真空絶縁碍子の性能向上が求められ続けます。今回紹介したポイントを押さえて実践すれば、必ず良い結果につながりますよ。